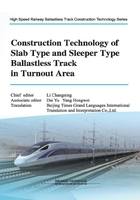
3.4 Construction Technology and Technical Requirement for Turnout Slab Laying
3.4.1 Turnout slab storage,transportation and site acceptance
1.Turnout slab transportation and loading and unloading
Turnout slabs shall be transported on road.The turnout slab shall be separated with the truck with cushion blocks.The lowest cushion block layer shall be fixed on the heavy trucks,and every layer of cushion blocks shall be vertically aligned,the position and quantity of supporting points shall comply with design requirement.Cushion blocks shall be set with antiskid rubber mat to prevent the turnout slab from sliding during transportation.The turnout slabs shall be protected properly in transportation,overspeed must be forbidden,smooth road shall be selected and avoid excessively bumping.The turnout slabs shall be loaded and unloaded with special lifting device,bumping,falling and crashing are strictly forbidden.
2.Turnout slab storage
The turnout slabs,after arriving at site,shall be stored at track position or main track by crossing the packway at both sides of the subgrade(note:the slope road temporarily set at one side or both sides of the subgrade,and is of certain included angle with subgrade direction),for easy laying construction of turnout slabs.
Before storage,the graded broken stone on subgrade surface layer shall be completed construction,bearing capacity and water prevention and drainage conditions satisfy storage requirement and have been qualified acceptance.Two rows of timber piers shall be used to support the turnout slabs for storage,with maximum two stacking layers.4~6 cushion blocks shall be place between turnout slabs and the storage foundation,as well as between every layer of turnout slabs.The cushion blocks shall be vertically aligned,their specification,size and supporting point position shall comply with design requirement,the allowable deviation for cushion height is ±2mm,and the bearing surface shall be parallel with each other.
3.Turnout site acceptance
No.18 and No.42 high speed turnout slabs shall be produced by prefabrication factory,and they shall be accepted before arriving at the site.The acceptance includes specification,model,overall dimension,concrete appearance quality,whether the embedded casing pipe is in good state,and the ex-factory certificate shall be inspected.Those non-corforming products shall not be accepted.
3.4.2 Rebar laying for turnout slab base
1.Laying of cushion block for protection layer.The protection layer cushion block of rebar base shall be constructed on concrete cushion.The size of protection cushion block is 35mm×50mm×400mm,35mm×400mm this side lies below,the cushion block shall be arranged as per longitudinal spacing 500mm and transversely spacing 400mm,and rebar shall be ensured to lay on spacing-fixed cushion blocks.
2.Rebar laying.Rebar shall be bound and constructed according to the position marked by inked line beforehand,the position of shear rebar on turnout slab shall be marked,the shear rebar position shall be reserved in rebar binding operation,to avoid rebar overlapping in slab rough laying and influencing the turnout slab installation in place accordingly.The longitudinal ф25mm rebar shall be arranged along the track,transverse ф12mm rebar(some ф25mm rebar in cross-over track area)shall be vertically arranged with longitudinal rebar,longitudinal rebar at upside while transverse rebar at downside,the spacing for among longitudinal and transverse rebar shall be arranged as per design requirement,the thickness of concrete protection layer at foundation is 30mm,and the thickness of lateral protection layer is 50mm.The longitudinal of ф25mm single longitudinal rebar is 12m,one 6cm long casing pipe shall be used for mechanical connection,the mechanical connection length for a single casing pipe shall not be more than 36m,the jointing percentage for a single cross section shall not be over 50%.The mechanical connection length for a single casing pipe shall not be more than 36m,overlapped connection is 1.1m,the jointing percentage for overlapping connection shall not be over 50%,and the overlapping area shall be away from high walls.When longitudinal or transverse rebar clash with middle heightened cushion blocks,the rebar spacing shall be appropriately adjusted to ensure cushion blocks stable and in correct position.
3.4.3 Rebar insulation binding
Rebar binding shall adopt plastic edge insulators,model is 25-12“+”type,25-25“-”type,25-25“+”type,12-12“-”type.Rebar shall be insulation tested after binding,the insulation resistance between longitudinal and transverse rebar shall not be less than 2mΩ.Crack prevention rebar network shall be bound after turnout slab rough laying.Foundation rebar for railway switch shall be embedded by means of drilling holes,with drilling hole depth 580mm,then shall be bound as per design spacing.
The formed rebar network shall be insulation inspected,the required insulation resistance shall be of 2mΩ and above.
3.4.4 Concrete cushion block installation and isolating wall pouring
According to the position of concrete cushion blocks which are set out in advance,one 20mm thick mortar layer shall be paved at bottom side,then concrete cushion blocks shall be installed on the mortar,the plane position and height of the cushion blocks shall comply with design requirement.The leveling rod shall be used to control the flatness of cushion blocks in cushion block installation.The position error for cushion block installation transverse ±3mm,longitudinal ±5mm and height ±5mm.the spacing of the rebar can be appropriately adjusted which may influence the installation of cushion blocks.
According to the angular point position of slab,the concrete formwork for isolating wall shall be erected,the isolating wall shall be poured with C40 concrete,the width of isolating wall is slab gap width plus 10cm,and shall extend 5cm respectively to slab at both sides.Height precision shall be controlled within ±5mm.After construction of concrete isolating wall for turnout slab,it shall be cured according to related requirement.According to CP Ⅲ ,GRP point shall be surveyed with total station free setting station polar coordinate method,the central point of every turnout slab joint shall be marked,and a hole with 20mm diameter and 100mm depth shall be drilled on the central point,anchor rod shall be installed,at the same time,the datum mark(GRP point)copper nail shall be pre-embedded,the allowable deviation of GRP point place positioning is ±5mm.when concrete has reached certain strength and stability,the precise coordinates of the datum mark(GRP point)shall be measured,the measured result shall be adjustment processed with adjustment software,the required adjustment precision:plane ±0.2mm and height ±0.1mm,which shall serve as the station setting point and locating point for turnout slab fine adjustment.
3.4.5 Turnout slab rough laying and fine adjustment
Before turnout slab rough laying,double-layer wood blocks shall be temporarily placed at four angular points of the turnout slab.The turnout slabs shall be hoisted and put down slowly to laying position by crane.The turnout slabs shall suspend falling 1.5m away from concrete cushion.The turnout slab laying personnel shall check whether bolt sleeve and gantry rebar are in good condition beneath the turnout slab.
Rough playing position inspection:the turnout slabs position shall be inspected after laying,error shall be calculated based on comparison between triangular belt coordinate point and triangular groove of the turnout slab which have been set out by measuring group,and the turnout slabs shall be adjusted according to the error until the rough laying precision of the turnout slab satisfy the requirement.
Fine adjustment claw installation:The fine adjustment claw shall be installed after rough laying of turnout slab.Firstly the fine adjustment claw shall be adjusted to make its transverse,longitudinal and height stroke at 1/2.Then the plastic protective jacket on the bolt hole of turnout slab shall be taken out,the fine adjustment claw shall be installed and closely attached to the lateral side of turnout slab.
Once fine adjustment claw is installed,its high bolt shall be adjusted to make the fine adjustment claw closely attach to concrete cushion block.After 4(or 6)fine adjustment claws are securely fixed on concrete cushion blocks,the fine adjustment claws shall be adjusted simultaneously,the concrete cushion block shall be loaded with stress,turnout slab shall be lifted by the supporting of concrete cushion block,and the wood blocks for temporary supporting can be taken out.
3.4.6 Turnout slab fine adjustment
The prism three-dimensional coordinates shall be measured on four angular points surveying plate of turnout slab with the total station which complies with precision requirement,through quick systematic comparison of total station fine adjustment,the adjustment for three-dimensional directions can be determined,then the three-dimensional adjusting function of the fine adjustment claw shall be applied for gradual adjustment,until reaching the designed theoretical position and height.
The forced alignment tripod of the total station shall be place on GRP datum mark between turnout slabs,station shall be set and aligned by using the datum mark(station setting position shall be 6~25m away from tight aligned turnout slab),at the same time,the rearview prism shall be place on GRP datum mark and leveled by using the forced alignment tripod.The total station,by applying one prism point and corresponding datum mark on the straight rail of track slab which has been tightly aligned in place,will realize its orientation.After orientation precision meeting the requirement,the tight aliment can be performed.
Fine adjustment data surveying:total station is erected on track datum mark,through quick surveying system,the actual three-dimensional coordinates of the prism will be measured on 4(or 6)locating holes of the turnout slab which is being adjusted,by comparison of the prism point theoretical coordinates input the computer beforehand with the actually measured coordinates,the deviation value will be real-time displayed on the screen for quick fine adjustment system.
Turnout slab fine adjustment:The lateral turnout slab in the whole group of turnouts shall be tightly aligned in turn from tail side to head side,the turnout slab at track cross-over shall be tightly aligned from cross-over to both ends,and the allowable deviation for turnout slab fine adjustment is shown in Table 3.
Table 3 Allowable Deviation for Turnout Slab Fine Adjustment

3.4.7 Base self compacting concrete pouring
The formwork shall be erected according to base plate sideline,and both sides of the base shall be 220mm wider than turnout slab.The formwork shall be erected perpendicularly,firmly and smoothly,the slab staggering for adjacent formwork shall not be more than 1mm,the formwork joint shall be pasted with double faced adhesive tape to ensure tight sealing,and the bottom formwork shall be sealed with mortar to ensure not leakage.20mm soft fiber cushion shall be installed between the external side of concrete cushion block and the formwork.The formwork shall be 200mm higher than the top surface of turnout slab at the pouring mouth for self compacting concrete;and formwork shall be 15mm higher than bottom surface of turnout slab at mortar outlet.
In order to ensure displacement and floating do not occur for the turnout slab which has been tightly aligned during self compacting concrete pouring process,the withholding device shall be installed at both sides of turnout slab and between slabs before pouring.The reinforcement of withholding device between slabs is perpendicular to concrete cushion,holes shall be drilled by portal electric drill,instant adhesive shall be poured into,the reinforcement position shall be in the middle of turnout slab joint,longitudinal error is ±20mm,transverse position shall try to avoid crash with GRP point,the upper steel channel shall cover on turnout slab,and the turnout slab shall be protected by placing steel plate on the contact surface of steel channel and slab.The spacing of lateral withholding device shall not be more than 3.7m.the withholding force shall be realized by anchor rod and angle bar,the reinforcement depth of anchor bar shall reach over 10cm,and its pulling resistance shall not be less than 30 kN.
Self compacting concrete shall be poured from single side of turnout slab.Concrete,falling down from tank truck onto chute,shall be poured through the chute,the chute length shall not be less than 1.5m,and free falling height shall not be more than 1.0m.The transfer hopper can be adopted for pouring where concrete tank truck fails to arrive at.Concrete tank truck delivers the self compacting concrete to the transfer hopper,the transfer hopper will be delivered by the crane,and then pouring can be performed by the chute.
Self compacting concrete is not suitable for quick pouring,the charging continuity and continuous fluidity of concrete mixture on turnout slab shall be ensured,and pouring time shall be 10~15min.When concrete surface is 15mm higher than turnout bottom surface,the concrete flow rate can be checked through observation hole,so as to control concrete pouring speed.The floating mortar shall be scooped out by workers nearby.The residual concrete shall be removed immediately once pouring is completed.
Self compacting concrete,once pouring is completed,shall be cured immediately,and the curing time shall not be less than 14 days.During curing period,the concrete shall be covered by geotextile,sprayed with water to keep moisture.
In order to increase work efficiency,the shunting machine foundation and the base for each turnout group shall be formwork erected and poured simultaneously.
3.4.8 Formwork dismantling and curing afterwards
When concrete strength reaches 5 MPa,the fine adjustment claw and formwork can be removed.In formwork removal,the edge and corner of concrete shall not be destroyed.Once formwork is removed,the concrete shall be cured immediately until required curing duration.
The formwork,after being dismantled,shall be cleaned and painted with grease.Formwork,lateral support and withholding device shall be stored in category.