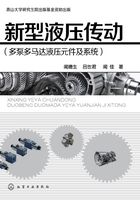
第六节 开路式泵的噪声及控制方法
由于近年来工业自动化的进展,使液压技术向高压化、高速化、大功率化方向发展,这样也就给液压系统和液压元件带来了一个重要的问题——噪声问题。本节将以斜盘型泵为例讨论柱塞泵的噪声及控制方法。
一、闭路式泵降噪结构存在的问题
在轴向柱塞泵中能使泵产生噪声的噪声源很多,开路式斜盘泵也是一样。这里着重讨论斜盘型轴向柱塞泵由于闭死容积所产生的噪声及控制方法。
斜盘型轴向柱塞泵在配流转换过程中压力变化性能的好坏,是决定泵的噪声性能好坏和工作可靠性的重要因素之一,也是泵中产生烧盘现象的主要原因之一。即使泵的其他部位设计得再好,若此过程未解决好,则泵也不能很好地正常工作。改善配流过程性能的基本方法,就是对柱塞腔中的液体实行预压缩和预膨胀,使柱塞腔内的压力逐渐过渡到配流口(输出口或吸入口)的压力。这样可以消除由于液压油压力不同(这里指的是柱塞腔与配流口的压力)而引起的噪声和振动。泵在不同工况下工作时,因工作压力不同(对于恒压泵好一些)而不易实现完全的预压缩和预膨胀,也就是说在不同的过压缩和欠膨胀,或是欠压缩或过膨胀过程中,柱塞泵将产生不同程度的振动和噪声。
以上问题的主要原因是变量泵变量倾角的变化和工作压力变化所引起的,目前已有很多较为理想的解决方案,如三角槽法、阻尼孔法以及其他方法,但这些方法大都只适用于定量泵,对于变量泵,这些方法就不太适用了。变量泵与同规格的定量泵相比,其泵的噪声要大些,一方面是由于变量轴向柱塞泵中斜盘及变量机构所引起的机械振动和力不平衡所产生的噪声;另一方面是由于变量轴向柱塞泵中配流盘处配流过程中压力冲击引起的噪声。目前已有的降噪方法一般是在变量轴向柱塞泵的直立的配流盘上采取各种办法。但这些办法一经设计完后就不能变了,即不会随变化的流量而变化,所以不能满足变量轴向柱塞泵中降噪的要求。
由于闭路式轴向柱塞泵的原理和结构所限,上述问题不能得到圆满的解决,所以,我们在开路式斜盘型轴向柱塞泵上采用了一种新型的降噪结构,并将其应用于25KZB、63KZB、250KZB、400KZB以及双级串联轴向柱塞泵上,收到了满意的结果。这种结构是在开路式斜盘型轴向柱塞泵的斜盘上开减振槽的方法,使减振效果跟随流量变化而变化,达到最好的减振降噪效果,也就是说使泵始终处在最佳的理论状态。
1.困油噪声的产生
闭路式轴向柱塞泵在工作中,缸体旋转,配流盘固定,斜盘倾斜放置,必然有一侧处在高压区,另一侧处在低压区。随着缸体的转动,柱塞在缸体内做往复直线运动。由斜盘、滑靴、柱塞、缸体及配流盘组成的控制腔室,通过配流盘控制泵的吸压油过程。
图2-106是对称正遮盖型配流盘的工作状态。图中点A、B分别为上、下止点的位置,p0、ps分别为低压腔和高压腔的压力。α'为缸体配流窗口的范围角。αf为配流盘上两个配流窗口间的夹角,ω为缸体的旋转角速度,φ为缸体与柱塞、滑靴自上止点开始的转角。

图2-106 对称配流盘的工作状态
当缸体旋转,缸体配流窗口刚刚与配流盘低压腔脱离,柱塞容腔形成封闭的容腔,这时柱塞工作腔的压力与配流盘低压腔的压力相等。缸体继续转动,由于斜盘的作用,柱塞运动使柱塞容腔扩大,其中的压力稍低于低压腔的压力。转过Δφ1后,到达A点,柱塞工作腔开始压缩,随着体积的减小,容腔内的压力开始升高,升高到某一值时,突然与配流盘的高压腔的压力ps接通,这时柱塞腔内的压力骤然上升至高压腔的压力,从而引起压力冲击。压力冲击值为:
(2-197)
式中 E——油液的弹性模数,Pa;
V——缸体孔内的容积,m3;
dV,lV——柱塞窗口直径与长度,m;
v0——液体的运动黏度,m2/s。
如图2-107所示,由于高压油突然进入封闭的柱塞工作容腔,其中的油液被突然压缩,引起高压油的倒流,从而产生振动和噪声。同样由高压腔向低压腔转换时,缸体配流窗口转过下止点,柱塞容腔由于柱塞的运动使容积增大,柱塞工作容腔的压力下降,下降到某一值时(高于低压腔压力)突然与低压腔接通,柱塞工作容腔的高压油向配流盘的低压配流窗口处膨胀,释放能量,产生瞬间的压力冲击,在短时间内,柱塞工作容腔的压力低于泵的低压腔压力。由于压力冲击而产生的强烈振动和噪声,会降低泵的寿命,破坏流量的均匀性,一般情况下,这种结构的轴向柱塞泵(大流量的)在20MPa的压力下工作时,噪声值可达90dB以上。为了避免和减小上述现象,目前生产和使用的轴向柱塞泵常采用下面几种基本方法,进行困油区的降噪结构设计。

图2-107 泵闭死容积对压力的影响
①使柱塞工作油腔处于闭死压缩或膨胀状态,靠柱塞的运动使容积压缩或膨胀闭死油液的体积,从而达到预升压或预释压的目的。
②用开减振槽或减振孔的办法,将高压油慢慢引进或放出,使柱塞工作容腔的压力慢慢地向待接通的配流腔过渡。
③将上述两种方法联合在一起使用控制噪声的方法。
④将配流盘转过一个角度的方法。
2.目前的困油区降噪结构存在的问题
图2-108是采用闭死压缩和闭死膨胀的方法进行预升压和预释压的降噪结构。

图2-108 配流盘预升压和预释压结构
在闭死压缩区,当缸体配流窗口与配流盘低压腔脱离时,缸体配流窗口刚好位于上止点位置,当缸体继续转动时,柱塞工作容腔进入闭死压缩区,经过闭死压缩范围角Δφ1后,柱塞工作容腔的压力正好升到配流盘的高压腔压力ps,这时柱塞的闭死容腔与配流盘的高压腔开始接通。
在闭死膨胀区,当缸体配流窗口与配流盘高压腔脱离接触时,缸体配流窗口正好位于下止点位置。缸体继续转动,柱塞工作容腔进入闭死膨胀区,经过闭死膨胀范围角Δφ2后,柱塞工作容腔压力正好降为配流盘低压腔压力p0,这时,柱塞的闭死容腔与配流盘的低压腔开始接通。
采用上述方法进行闭死压缩和膨胀的预升压、预释压计算式为:
预升压值Δpc为:
(2-198)
预释压值Δpi为:
(2-199)
写成无因次参数表达式为:
(2-200)
(2-201)
式中 γ——斜盘倾角,rad;
γe——额定工况下的斜盘倾角,rad;
V0e——额定工况下的柱塞容腔的无效容积,m3。
流量与压力变化如图2-109所示。

图2-109 流量与压力关系
由上面的讨论可以看出:
①上述方法设计的困油区降噪结构,不能适应压力变化的工况要求,当泵的工作压力变化时,相应于额定工况压力的闭死压缩角和闭死膨胀角(Δφ1和Δφ2)便不能适应了。对于这种情况,一方面应使设计压力值尽量满足在各种使用压力附近;另一方面,可以用工作压力控制配流盘的错配角,使Δφ1和Δφ2随工作压力的变化而变化。但这必将导致泵的结构复杂。本节仅讨论泵在额定压力下的工作情况。
②上述方法设计的困油区降噪结构,同样不适用变量泵的要求,即当泵的输出流量变化时,因为柱塞工作腔的升压和释压(Δpc和Δpi)是排量的函数,也就是说是斜盘倾角γ的函数。因此,对于确定的闭死压缩角和闭死膨胀角Δφ1和Δφ2,当斜盘倾角γ脱离实际设计值时,其降噪和抗冲击效果会受到影响,甚至还会对泵产生冲击。如当斜盘倾角γ<γe时,在上止点的柱塞容腔处是欠升压状态,也就是柱塞工作容腔由于闭死压缩,其压力值还未升高到配流盘的高压腔内压力时,闭死压缩过程就结束了,柱塞工作容腔即与配流盘高压腔接通产生压力冲击。同样,在下止点处,柱塞工作腔将处于欠释放状态,也就是说,当闭死膨胀结束时,柱塞工作容腔的压力还未降到配流盘低压腔的压力,便与配流盘的低压腔接通了。这时柱塞工作腔内的低压油向配流盘的低压腔内膨胀,引起油液倒流,产生压力冲击。当γ>γe时,柱塞工作腔会产生过升压和过释压的现象。过升压和过释压同样会引起柱塞泵的压力冲击现象。
在配流盘上开减振槽或减振孔的降噪结构,其柱塞工作腔的预升压和预释压值同样与斜盘的倾角γ有关,当γ<γe时,或γ>γe时,柱塞工作容腔内同样会产生欠压或欠释压,或过升压或过释放压的现象。但这种结构与单纯的闭死压缩和闭死膨胀结构相比有所不同,其不同之处如下。
①通过减振槽(或减振孔)注入柱塞工作容腔(或由柱塞工作容腔泄出)的油液,与靠柱塞运动使柱塞工作容腔压缩(或膨胀)相结合的办法,可以使预升压(预释压)所需的预压缩角(预膨胀角)比单纯靠闭死压缩(膨胀)方法所需要的预压缩角(预膨胀角)减小。
②由于减振孔与排油腔(或吸油腔)相通,当柱塞工作容腔压力与配流盘配流窗口内压力不等时,液体通过减振孔的流动就不会停止,两者差别越大,流过减振孔的流量也就越大,因而柱塞容腔内压力上升(或下降)的速度也越快。这就使得柱塞工作容腔内的压力与配流盘配流窗口的压力很快接近(但不是突然接近)。当工况发生变化时,如负载压力高于额定压力,柱塞工作容腔在接近排油腔时,两者压力差比额定工况时大,就使由减振孔注入柱塞工作腔的流量比额定工况同一位置时大,直到两者压力接近,流经减振孔的注入流量变小,柱塞工作容腔内压力上升速度随之减慢,因而,当柱塞工作容腔与配流盘排油腔相通时,两者压力相差不大。
因此,这种结构对偏离设计点太大的情况适应性不好,仍然会出现较大的压力冲击,产生较高的噪声。
至于将配流盘转一个角度的方法,只是解决了正配流盘中的闭死区工作容积的再压缩和再膨胀问题。
将以上几种方法合在一起应用,仍不能解决泵在变排量下实现完全的预压缩和预膨胀,因此,对于变量轴向柱塞泵,采用困油区降噪结构来控制轴向柱塞泵的噪声是不尽合理的。
二、开路式泵上的一种新型降噪结构
1.开路式泵在斜盘上开减振槽结构
由上述讨论可知,为解决由于配流而产生的压力冲击现象,在闭路式轴向柱塞泵配流盘上开卸荷槽或采用闭死压缩或闭死膨胀方法不能适应变排量工况的要求,即使柱塞工作容腔的压力预升压或预释压到某一值,所需的闭死角或卸荷槽范围角都是斜盘的倾斜角γ的函数,而配流盘的结构一旦确定,闭死角或卸荷槽的范围角以及其他尺寸参数便随之确定。当输出流量变化时,即斜盘倾角γ变化时,预压缩或预释压值就偏离设计点,影响降噪的效果。
开路式轴向柱塞泵有两块配流盘,即直立配流盘和倾斜配流盘,这种泵的配流结构为解决上述问题提供了便利条件,特别是出现了斜盘配流。
在开路式轴向柱塞泵的倾斜配流盘(斜盘)上,滑靴运行是一椭圆形轨迹,即:
(2-202)
对于每一倾角γ,就有一条相应的椭圆轨迹。设对于某所需要的预升压值(或预释压值)其需要的闭死角为φ,则:
(2-203)
由上述方程可知,对于每一个倾角γ,就有一个闭死角与之相对应。因此,在每一条椭圆轨迹上,有不同的闭死角φ,这些闭死角位置组成一条曲线:
(2-204)
如果在由低压到高压侧,或由高压到低压侧的配流转换中,柱塞工作容腔与配流盘配流窗口按上述曲线位置接通,柱塞工作容腔内的预升压值(或预释压值)便能满足变量输出工况的要求。
2.上止点闭死压缩区的情况
(1)求适应排量变化要求的闭死压缩位置
如图2-110所示,在上止点处,缸体配流窗口与配流盘低压腔相切[见图2-110(b)中A'的位置处]滑靴油室也刚好与斜盘上的低压配流腔相切。图2-110(a)中A处的位置,由柱塞、滑靴、斜盘、直立配流盘及缸体所组成的腔室(简称为柱塞工作容腔)形成闭死容积。此时柱塞工作容腔压力等于配流盘低压腔压力p0。当缸体继续转动时,柱塞往复运动的结果使柱塞工作容腔内闭死容积被压缩,柱塞工作容腔内压力升高,设当斜盘倾角为γ时,柱塞工作容腔压力升高到所需要的高压腔压力ps时,所需要的闭死压缩角为φ,缸体转过闭死压缩角φ后。柱塞工作容腔与配流盘高压腔相通,如图2-110(b)所示。

图2-110 滑靴和缸体与配流盘相对位置
设当γ=γ1时,压力升至ps所需的闭死压缩角为φ1;当γ=γ2时,柱塞容腔内压力升至ps所需的闭死压缩角为φ2,则相应的滑靴运动轨迹为:
C1:
(2-205)
C2:
(2-206)
图2-111所示为C1、C2轨迹图。

图2-111 滑靴运动的椭圆轨迹族
(2)求适应排量变化要求的闭死压缩位置φ=f(γ)
根据流体连续方程:
(2-207)
式中 V01——φ=0时柱塞工作容腔的闭死容积;
K——液体体积弹性模量,Pa;
dV——容积增量,L。
容积增量包括柱塞运动使柱塞工作容腔压缩体积dV1、泄漏的体积dV2,即:
(2-208)
而
泄漏体积dV2包括四部分:配流盘两端面的泄漏;滑靴副间的泄漏;柱塞与缸孔间的泄漏;球铰副间的泄漏。
下面分别计算。
a.配流盘两端面的泄漏:
配流盘与缸体端面之间的流动属于压差流动,可直接用下式计算:
(2-209)
式中 Δp——压差,Pa;
——综合系数,
按下式计算:
(2-210)
式中 h'1——端面间的间隙,m;
R1,R2,R3,R4——配流盘密封带尺寸,m;
μ——油液动力黏度,m2/s。
配流盘与缸体端面间除压力差流动外,还有缸体相对配流盘的转动,属二元流动。
根据连续性方程(采用极坐标):
且有:
(2-211)
解上述微分方程,设:
则:
代入微分方程式(2-211)得:
(2-212)
(2-213)
分别解上述微分方程得:
(2-214)
式中 C1,C2,C3,C4——常数。
边界条件:
如果考虑配流副间油液的挤压流动,即配流盘与缸体之间的油膜厚度不断变化,配流盘与缸体之间还有一个速度为的相对运动。因此,配流盘与缸体端面间的流动属三元流动,这里只按二元流动计算,不计
项。
b.滑靴副间的泄漏:
(2-215)
式中 Cl2——泄漏系数。
滑靴副间的流动除了在压差Δp作用下的压差流动外,还有滑靴在斜盘上的沿椭圆轨道运动的影响。另外,滑靴在轴线上绕自身轴线的转动,如果考虑油膜的挤压效应时,滑靴与斜盘之间还有一个速度为的相对运动。在上述因素影响下,滑靴与斜盘间的油膜及液体的流动也属于三元流动。
c.球铰副间的泄漏:
(2-216)
式中 h3——球铰副的间隙,m;
θ1——滑靴与柱塞球头的外包络角,rad;
θ0——滑靴与柱塞球头的内包络角,rad。
d.柱塞与缸体柱塞孔间的泄漏:
柱塞与缸体柱塞孔之间的泄漏流动,包括在压差Δp作用下的缝隙流动及柱塞相对缸体柱塞孔往复运动引起的托动流动:
(2-217)
式中 v——柱塞与缸体孔间相对运动速度,m/s;
d——柱塞直径,m;
h4——柱塞与缸体孔间的径向间隙,m。
除上述运动外,柱塞在缸体孔内还有相对的旋转运动和由于偏载而引起的倾斜,故实际上也是三元流动。
如果不考虑各运动副间的相对运动,仅考虑压差对泄漏的影响,则上止点闭死压缩区的方程如下:
(2-218)
式中 h1,h2,h3,h4——间隙。
由上面讨论可以看出:实际工作中,滑靴副两接触面间的流动、配流盘与缸体两端面间的流动、柱塞球头与滑靴间的流动以及柱塞与缸体孔间的流动,均属于三元流动,流动情况相当复杂。为便于计算,这里还是采用传统的计算方法,即不计泄漏的影响,由泄漏所造成的影响可以采用计算中加以修正的方法解决,是完全可行的。
如果不计入泄漏的影响,则:
(2-219)
代入边界条件:
得:
(2-220)
式中 V0——斜盘倾角γ=0时的闭死容积,m3。
当斜盘倾角由0°~20°变化时,滑靴的运动轨迹是相应的椭圆:
建立极坐标,求上述轨迹在极坐标下的方程。取斜盘中心即直角坐标系原点为极点,oy轴为极轴,见图2-112,由椭圆参数方程:
(2-221)

图2-112 滑靴运动的椭圆轨迹
可得到极点在坐标原点o处的极坐标方程:
(2-222)
3.实际工作曲线
在上述计算中,均以滑靴中心作为基准考虑闭死压缩角φ,而实际工作中,滑靴中心沿椭圆轨迹运动时,滑靴内密封带圆周首先与倾斜配流盘的配流腔接通,因此,上面所求的实际工作曲线应是所求理论曲线。图2-113、图2-114所示为理论曲线的包络线。
(2-223)

图2-113 滑靴中心的理论曲线

图2-114 实际的包络线
C1—理论曲线;C2—所求包络线;rγ—滑靴内密封带半径,m;φ1—理论曲线极角,rad;γ—理论曲线与包络线的向径夹角,rad;λ—理论曲线向径与该点法线之间的夹角,rad
λ可用下式表示:
在△BOC中:
考虑到λ为负值的情况,如图2-114(b)所示,同样可求得理论曲线C1的包络线C2的方程。
因此,包络线C2可用下述方程表示:
(2-224)
同理,考虑下止点到闭死膨胀区的情况,可得到下面方程:
代入边界条件:
(2-225)
其中
因此得理论曲线方程为:
(2-226)
包络线方程同样可根据式(2-226)求得。
上面计算得出了倾角γ=0°~20°时单独采用闭死压缩和闭死膨胀,使柱塞工作容腔闭死容积内的油液压力升高或降低到高压腔压力或低压腔压力时所需的闭死角,对应这些角度,可得到一条适应所有γ角变化的曲线。
考虑一般情况下常用的工况:斜盘倾角γ=5°~20°的变化范围。
在γ=5°~20°变量范围内,由上面计算结果得到一条相应的包络线。
当γ=γmin=5°时,φ=φmax,ρ=ρmin。
γ=γmax=20°时,φ=φmin,ρ=ρmax。
即当γ=γmin时,所对应的闭死角为φmax。
当γ=γmax时,相应的闭死角为φmin。
当斜盘倾角γ在5°~20°范围内变化时,柱塞工作容腔沿上述曲线接通。
考虑滑靴和斜盘的结构,如果闭死膨胀结束后,柱塞容腔直接与配流盘配流窗口接通,这一曲线段的连通槽面积必须足够大,大到其节流作用对柱塞工作容腔压力的影响可以忽略不计。而这个连通槽面积的加大,会导致连通槽处轮廓线沿直径方向外移,以致超出滑靴处密封带范围,引起泄漏,因此,考虑滑靴最大密封带的限制,必须采用宽度较小的三角槽过渡。另一方面,采用三角槽过渡可以减少闭死范围角。
三角槽可看作一个节流口,即当滑靴油室经过三角槽范围时,柱塞工作容腔会产生预升压和预释压,换而言之,三角槽区可以承担一部分预升压或预释压任务。
下面分别考虑上止点预压缩和下止点闭死膨胀区的情况。
(1)上止点预压缩区
考虑倾斜配流盘的结构,斜盘上只有低压配流口。因此,上止点预升压区的减振槽开在斜盘低压配流槽上。随着斜盘倾角(γ=5°~20°)的变化,滑靴经过上止点后,与配流盘低压腔脱开的位置沿所求曲线而变化。
当γ=γmax时,油室从上止点与斜盘低压配流腔脱开,开始闭死压缩,经过φmax后,闭死压缩结束,柱塞工作容腔压力升高到配流盘高压腔压力。
当γ=γmin时,滑靴油室在上止点附近与斜盘低压配流腔脱开,开始闭死压缩,经过φmin后闭死压缩结束,柱塞工作容腔压力升高到配流盘高压腔压力。
当斜盘倾角为γ时,单独闭死压缩所需的闭死角为φ,即滑靴油室在上止点附近,由曲线AA'上的A'点开始与斜盘低压配流腔脱开,如图2-115所示,进行闭死压缩,经过闭死压缩范围角φ'后,压力升高到配流盘高压腔压力,与配流盘高压腔接通。考虑减振槽后,由于减振槽卸荷一部分压力,滑靴油室与配流盘高压腔接通的位置发生变化。

图2-115 实际包络线
当斜盘倾角为γ时,滑靴油室经过三角槽区,在A'点与三角槽脱开,开始单独闭死压缩,经过闭死压缩范围角φ'后,与高压配流腔接通。
在减振槽范围内,滑靴油室在A点进入卸荷区。一方面,由于柱塞运动使柱塞工作容腔内压力增加,另一方面,由于连通槽的作用,释放掉一部分压力。滑靴油室在上止点与低压腔脱开时,压力等于低压腔压力,经过三角槽后,压力升至p'0,再经过单独闭死压缩区φ',压力升至ps。
下面根据流体连续性方程,考虑滑靴油室经过卸荷槽区的工作情况。
流体连续性方程为:
(2-227)
式中 V01——t=0时柱塞工作容腔的闭死容积,m3;
K——油液的弹性模量,Pa;
dV——容忍容量(增量),m3。
(2-228)
式中 V0——γ=γmax时的闭死容积,m3。
(2-229)
(2-230)
式中 dV3——泄漏体积(暂不考虑),m3;
dV2——通过卸荷槽流出的体积,m3。
(2-231)
式中 Cq——流量系数;
Sx——节流面积,m2。
对于三角减振槽,有:
(2-232)
图2-116所示为三角槽结构,所以:
(2-233)
设
(2-234)
(2-235)

图2-116 实际三角槽结构
解上述微分方程式得:
(2-236)
(2-237)
(2-238)
代入边界条件:
(2-239)
考虑单独闭死压缩区的情况,根据下列方程:
(2-240)
代入边界条件:
(2-241)
联立
(2-242)
即可求解三角槽的范围角。
(2)下止点闭死膨胀区
考虑卸荷槽的作用,当斜盘倾角为γ时,柱塞工作容腔在下止点脱离配流盘高压腔,经过闭死膨胀角φ'后,压力降至p'0,这时柱塞工作容腔与卸荷槽接通,经过卸荷槽区δφ后,压力降至低压配流油腔压力p0,与配流盘低压配流腔接通,如图2-117所示。
同理可得到下面方程:
(2-243)

图2-117 下止点闭死膨胀区包络线
求解便可得到所需要的卸荷槽范围角。
4.结论
通过对开路式轴向柱塞泵上配流盘降噪结构的分析可得出以下结论。
在闭路式轴向柱塞泵直立的配流盘上开卸荷槽或闭死压缩(膨胀)的方法,不能适应变量工况的要求。目前闭路式轴向柱塞泵上配流盘降噪和抗冲击结构仅适应设计工况的要求,而当排量增大,导致斜盘倾角γ变化时,压力冲击和配流噪声将增大。
由于开路式轴向柱塞泵的结构特点是在泵的斜盘上开有配流槽,滑靴在斜盘上的运动轨迹随斜盘倾角γ变化而变化,所以在斜盘上开卸荷槽,能够使其降噪结构适应变排量工况的要求,即柱塞工作容腔内闭死容积与配油槽接通时的预升压值和预减压值可随斜盘倾角γ的变化(也就是随排量或流量变化)而变化。
三、轴向柱塞泵配油窗口面积对转速和噪声的影响
提高轴向柱塞泵的转速一直是泵研究人员重点面对的领域之一,大多数研究者都在材料、热处理、摩擦副设计上下功夫,主要解决材料的pV值、热处理硬度、摩擦副的润滑、支承力平衡等问题,以达到提高泵转速的目的。但事实上作为液压传动用的泵,以上研究是在过流面积很大时才是提高泵转速的关键问题,当过流面积很小时,进入控制容腔的液体流速过高的情况下,液体已达到空气分离压,更严重时达到饱和蒸气压,无论怎样改变材料、热处理,无论怎样设计摩擦副,泵都不能正常工作(这里是指无供油压力时的情况,有供油压力时除外)。这时配油窗口面积的大小将是影响泵是否可以提高转速的主要因素,因此我们对半开路式、闭路式、全开路式轴向柱塞泵进行了各种研究和试验。
1.开闭路式泵的试验简图
端面配油半开路式、闭路式、全开路式泵现场试验进出油示意图见图2-118~图2-120。

图2-118 端面配油半开路式泵现场试验进出油示意图

图2-119 端面配油闭路式泵现场试验进出油示意图

图2-120 端面配油全开路式泵现场试验进出油示意图
2.流量与配油窗口面积的关系
同样供油情况下,开路式为什么可以提高转速呢?这是因为在其他条件相同时,泵的进油速度只决定于泵的配流面积,即:
(2-244)
式中 v——配流口处液体流速,m/s;
A——配流口处面积,m2;
Q——泵的流量,L/min。
由上述试验可知,25KZB与25CY14-1泵所有的吸油处的阻力均相同,只是进油面积不同,对于25KZB泵有(下角标用K):
(2-245)
对于25CY14-1泵有(下角标用B):
(2-246)
由下面试验方法可知:
(2-247)
式中 A0——半开路式泵滑靴进油的面积。
当两种泵流量相同时,即:
(2-248)
(2-249)
而当液体流速相同,即
(2-250)
也就是说都达到最大的允许吸油流速时:
(2-251)
由式(2-250)和式(2-251)可知,端面配流全开路式泵可以提高一定的转速,这里忽略了泵壳内容腔的影响。
3.试验
为使试验做得比较合理,选定了齐齐哈尔第二机床厂阿荣旗分厂的一个试验台,泵入口到液面处的管径不变,并将开路式原理和闭路式原理用一个泵壳进行试验,实际上是只改变泵的内部零件进行试验比较。
为了说明问题,采用了25CY14-1A型泵和25KZB型泵进行试验。
首先进行端面配流半开路式泵的试验(注意此时液压油仅由斜盘处进入泵体和柱塞腔内)。当转速在1500r/min以下时,泵的噪声正常,流量40L/min,容积效率0.97,工作压力32MPa;当转速再增加,这时只要稍一提高压力,噪声就突然增加,而且无论转速怎样提高流量也不再增加了。
接着我们将开了进油口的斜盘和没开进油口的直立配流盘换掉,装上无进油口的斜盘和开有进油口的直立配流盘,这时就是25CY14-1A型泵,泵的进油口如CY14-1A接法,进行升速试验,其结果如下:当转速提高到2500r/min时,流量为66L/min,压力为32MPa,容积效率为0.95,完全满足部标,且噪声正常。当转速再提高时,泵的流量不再上升,加压时噪声突然变大。最后将开有进油口的斜盘装上,换下无进油口的斜盘,同时对泵进行升速试验。由于两端同时安装有进油管,泵两端同时进油,其性能如下:当转速提高到3700r/min时,泵的流量为100L/min,压力为32MPa,效率为0.95;当转速再增加,流量不变化,加压后,噪声就突然上升。为了与CY泵统一,我们又将斜盘处的进油口去掉,在泵壳内开流道,进行升速试验。转速为3500r/min,泵的流量为96L/min,压力为32MPa,容积效率为0.95时一切正常,当转速再提高,同样出现流量不再变化。加压后噪声发生突变。图2-121为流量与转速的关系;图2-122为流量与噪声的关系。

图2-121 流量与转速关系曲线

图2-122 流量与噪声关系曲线
4.结论
在无压供油条件下,所有工况相同,只有配油窗口面积不同时,可得以下结论。
①配油窗口面积越大,转速越高,全开路式泵高于闭路式泵,闭路式泵高于半开路式泵。
②配油窗口一定时,泵所能适应的临界转速是一定的。
③配油窗口一定时,到了临界转速后,噪声随转速的增高而增加,流量却不随转速的增高而增加。
④对于泵设计者来说,应对这一临界转速十分注意。