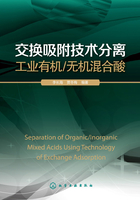
1.2 混合酸废水处理技术发展概况
现有的混合酸废水处理方法主要有:中和法、浓缩法、氧化法、萃取法、结晶法、化学沉积、离子交换、蒸发、膜分离法、吸附法、生化法等。这些处理方归纳起来可以划分为两大类,一类是将废水中的酸无害化处理或转化,但这类方法存在二次污染、处理成本高、资源浪费、需进一步处理、不能实现资源化重复利用等缺点;另一类是将其分离回收,处理后的水满足回用要求,实现废水的资源化。比较起来后一类更具有现实意义和发展前景,减少了含酸废水对生态环境的污染和破坏,实现了废弃物的再利用,大大降低工业过程用水量,实现了工业污水资源化、减量化、无害化。
1.2.1 混合酸废水处理技术
目前,混合酸废水的主要处理技术包括浓缩法、萃取法、膜分离法、吸附法或它们的组合工艺等。主要处理方法的研究现状介绍如下。
1.2.1.1 浓缩法
三氯乙醛生产过程中有废硫酸产生,其中H2SO4质量分数为65%~75%、三氯乙醛质量分数为1%~3%、其他有机杂质的质量分数为1%。用煤直接加热蒸馏,采用高温浓缩回收的浓硫酸无色透明,H2SO4质量分数大于95%[4];日本木村-大同化工机械公司采用搪玻璃管升膜蒸发和分段真空蒸发相结合,将废硫酸中H2SO4的质量分数从10%~40%浓缩到95%。加热过程采用高温热载体,温度为150~220℃,可将有机物转变为不溶性物质,然后过滤除去,该工艺可用于含多种有机杂质的废硫酸的处理[5]。有研究表明,近年来开发出了一种改进的浓缩法,称为气液分离型非挥发性溶液浓缩法。该法与高温浓缩法相比,蒸发温度低(50~60℃),蒸汽消耗量少,费用低(浓缩每吨稀硫酸耗电和蒸汽的费用约为30~60元)。国内对废酸的浓缩回收,通常采用钛质常压蒸发器或减压薄膜蒸发器。国外资料表明,废酸浓缩处理装置还可多功能应用,例如用于浓缩极难处理的废水,浓缩后与燃料混合焚烧。
目前,浓缩法存在于:①蒸汽、水耗量大,电耗量高,运行费用高;②处理量小,蒸发管道极易阻塞,运行不稳定;③材质要求高,设备投资大;④操作复杂,维修困难、费用高等问题。因此,废酸浓缩设备应向高效、节能、结构简单、操作维修容易、造价低、适应性强等方面发展。
1.2.1.2 萃取法
萃取法是以有机溶剂为萃取剂与酸充分接触,使酸在两相中转移,实现分离。对于萃取剂的要求是:①对于酸是惰性的,不与酸起化学反应;②酸或其他组分在萃取剂和水相中有很高的分配系数;③无毒,价格便宜,容易得到;④容易实现反萃,反萃时损失小。
对于废硫酸可以采用经C-I萃取剂萃取分离后,再依次用P-I吸附剂和活性炭吸附处理得到纯净的硫酸[6];以PCW-2萃取剂对γ酸(2-氨基-8-萘酚-6-磺酸)废水进行一级萃取,废水的COD去除率大于97%,萃取液用碱液反萃回收γ酸产品,每立方米废水回收4kg γ酸,回收产品中γ酸的质量分数大于96%,符合工业品质量要求,回收过程运行费用低,具有良好的经济效益和环境效益[7];以N235为萃取剂,氢氧化钠为反萃剂,进行萃取-反萃处理萘系染料中间体2-3酸(2-羟基-3-萘甲酸)生产废水,在最佳工艺条件下,一级萃取出水CODCr<200mg/L,萃取效率达96.5%。反萃效率100%,萃取剂可以循环使用不变性,有机物浓缩倍数可达270倍,CODCr约为7.2×105 mg/L[8];氨基-J酸是一种重要染料中间体,在其生产过程中酸化吸滤工段产生了一股废液,每吨产品约排放10t母液,该废水呈酱黑色,其中含硫酸500~700g/L,CODCr为35000mg/L左右,超过国家排放标准200多倍,且废水中的有机物大部分为毒性很高的多环萘胺类化合物,由于该废水中含有较高浓度的硫酸,用常规的叔胺类络合萃取剂处理含有磺酸基有机物废水的方法处理难度很大。通过用PCW25萃取剂对氨基-J酸废水进行萃取处理,废水的CODCr去除率>95%,萃取液用碱液反萃回收氨基-J酸产品,每立方米废水回收27.9kg氨基-J酸,回收产品符合工业品质量要求[9];溶剂萃取技术回收发酵液中柠檬酸,是利用发酵液中柠檬酸和其他杂质组分在萃取剂中溶解度的不同,把柠檬酸萃取到溶剂相中。然后,提高温度,用水对溶剂相进行反萃取,使柠檬酸重新进入水相,再经过离子交换、蒸发、结晶,最后得到产品。以葡萄糖等较纯净的物质作原料时,发酵液含杂质较少,可以用溶剂萃取法一次性直接提取柠檬酸[10]。国内常用的发酵原料多为木薯淀粉、甜菜糖蜜等,发酵液中含有大量的杂质,直接用萃取法提取柠檬酸效果不佳。而且为了有效分离柠檬酸,萃取与反萃取过程都采用连续多级逆流工艺,以保证有机相与水相的更好接触,多级萃取可使萃取收率达到90%;中药大黄的化学成分很复杂,其中具抗菌和抗癌活性的成分为大黄酸。制取工艺采用川大黄粉用20%硫酸于70℃在3h可完成结合态大黄酸的水解,以丙三醇作为助溶剂加入三氯甲烷中提取大黄酸,再用0.1% KHCO3萃取大黄酸纯度高于85%[11]。
萃取法虽然具有实现水相中酸的回收、萃取剂可反复使用、不消耗大量化工原料、节约热能等优点。但迄今为止,它的工业化应用还难以得到推广,主要原因在于:一是萃取体系复杂,工序复杂,需大量有机溶剂,萃取剂污染和毒性问题难以解决;二是络合萃取法的萃取剂和稀释剂容易流失至水相中,不仅使运行成本增加,同时还可能因潜在的有毒有机物造成新的二次污染;三是有机酸溶液的组成复杂,要求萃取剂有高度的选择性,能有效萃取酸而不萃取其他组分、无毒、化学性质稳定、价廉、易回收;四是在萃取过程中产生大量有机废水,生产成本高,反萃时仍有废弃物产生,如何对其进行处理也是一大难题。另外,萃取法常常因为有机溶剂中有毒物质的残留而不符合食品添加剂和医药卫生要求。这些都限制了这一方法的推广应用,寻求低价、高效、无毒的萃取剂仍然是萃取法研究的重要方向。
1.2.1.3 膜分离法
膜分离技术的分离介质为天然或人工合成的选择性透过膜,包括微滤、超滤、纳滤、反渗透等各种分离膜。膜分离技术是一门跨学科的新兴技术,它具有快速、高效等优点,特别适用于热敏性和生物活性物质的分离和纯化。近年来,膜分离技术已逐步应用于含酸废水和含酸产品的分离提取研究中,而且受到人们越来越多的关注。
钢铁工业中酸洗废液有硫酸、盐酸及硝酸/氢氟酸酸洗废液。目前应用于钢铁酸洗废液处理的膜处理技术,通过利用膜的离子选择性将铁盐和酸分离,同时回收酸和铁盐,处理过程无相变,有较高的经济和环保价值[12]。具体的膜处理技术根据酸的回收、浓缩以及废水排放等不同目的,可分为渗析法、纳滤法、气升式膜反应器法、膜蒸馏法等。钢铁酸洗废液的综合治理是世界难题,随着对膜分离理论及技术的研究不断深入,其在钢铁酸洗废液资源化处理和废水达标排放的应用亦会日益完善成熟[13,14]。现行的钢铁酸洗膜处理技术中,膜的性能、操作技术以及酸洗废液的特点是膜分离技术中的关键,对膜材料及应用技术进行深入研究是该技术广泛应用于实践的前提条件和主要发展方向。用阴离子交换膜渗析法处理含硫酸钠的高浓度硫酸废水,动态法分离废酸结果表明,H2SO4回收率达83.4%,回收酸中Na2SO4含量下降至5.2g/L[15]。化纤厂酸性废水大约含有质量分数10%的Na2SO4,7%的H2SO4,1%的COD。目前工厂的处理方法是加碱中和,兰化公司化纤厂废水产量3t/h,碱的消耗给企业带来很大的经济负担。采用扩散渗析法处理化纤厂酸性废水,回收率可达80%,回收酸与废酸的浓度比约70%以上,盐截留率70%[16]。
用阴离子交换膜回收废酸是工业中处理酸性废液行之有效的方法,理论上扩散渗析方法可以适用于任何产生废酸液的体系,除上面已经提及的几个工业应用领域外,还有诸如钛白粉工业、稀土工业、有色金属冶炼业、电镀业、木材糖化业等,其共同特点是废酸与盐离子的分离或纯化。但由于有些行业产生的废酸量大或废酸的浓度过低,用该法投资大或回收酸的浓度低,这些都限制了扩散渗析的使用。扩散渗析缺陷在于:一是处理量的限制,如一个500m2的扩散渗析器,一天仅能处理5~8m3;二是回收酸的浓度受平衡浓度的限制,即回收酸不能高于原料废酸的浓度;三是不能减少废液的排放量,回收后的残液仍不能直接排放[17]。
作为一种新型的分离技术,膜技术既能对废液进行有效的净化,又能回收有用物质,因此在酸性废液处理方面显示了广阔的发展前景。膜分离技术以电位差或浓度差为推动力,需热量少,不产生相变,可在较低温度和常压下操作,工艺简单,可回收大量有用酸、碱及金属。但膜技术应用仍存在许多问题,如膜制备困难、价格高、机械性能差、易污染、使用寿命低、浓差极化、能耗高、处理能力低等,多数仍处于中试或实验室研究阶段,工业应用较少。因此,迫切需要开发出新型膜材料,新的膜联合技术,使其优势互补,以便得到更广泛的应用。
1.2.1.4 吸附法
以往使用的吸附材料主要有活性炭、合成沸石、硅胶、活性氧化铝、活性白土等,近年来,合成吸附材料取得了很大进展,其中包括球形、高比表面积的大孔吸附树脂。吸附树脂又称聚合物吸附剂,它是以吸附为特点,对有机物具有浓缩、分离作用的高分子聚合物。其吸附机理为通过界面吸附、界面电性或形成氢键作用,对吸附物根据吸附力的不同及分子量的大小进行选择性吸附,然后在大孔吸附树脂上经一定的溶剂洗脱而达到分离的目的,具有物理化学稳定性好、吸附容量大、选择性好、机械强度高等优点[18]。
大孔树脂吸附法是成功应用于有机工业废水治理的资源化技术,废水在得到有效治理的同时并可回收一定量有用物质以抵偿运行费用。国内几十家生产DSD酸的化工企业对该废水只进行简单处理后直接排入江河湖泊中。针对DSD酸氧化工序生产废水的特点,采用南京大学环境工程系开发的对芳香族磺酸化合物具有特殊选择性的ND804大孔吸附树脂,对该废水进行了吸附-脱附一系列条件试验。废水经ND804树脂吸附处理后,CODCr由14790mg/L降至1300mg/L左右,COD去除率约为91%,并可回收纯度达80%的DNS酸,废水在得到有效治理的同时实现了废物的资源化[19]。树脂吸附法处理吐氏酸生产废水,用XDX-1大孔吸附树脂对吐氏酸生产废水进行动态吸附处理,废水经串联二级吸附后吐氏酸及其前体的浓度降低很多,精馏解吸液回收的吐氏酸及其前体可返回生产车间进行再生产,处理后废水经生化处理即可达到排放标准[20];NAD-50超高交联吸附树脂对水溶液中山梨酸的吸附能力明显优于CHA-111和XAD-4树脂。该树脂的表面极性和微孔结构在吸附过程中起决定作,pH值、温度、NaCl的存在和乙醇的质量分数对吸附有着很大的影响[21]。苯基周位酸生产废水含盐量高、色深、毒性大,难以生化降解,如不加以处理就直接排放,不但浪费化工原料,而且会严重污染环境。采用CHA-111大孔吸附树脂对苯基周位酸生产过程排放的汽提苯胺盐析废水和苯基周位酸酸析废水进行了吸附、脱附等处理工艺条件试验,取得了良好的处理效果[22]。
近年来大孔吸附树脂在天然产物化学成分的提取、分离纯化等方面有了较广泛的应用研究[23]。绿原酸是一种多酚类化合物,异名咖啡鞣酸,是植物在有氧呼吸过程中产生的苯丙素类化合物。绿原酸具有抗菌、抗病毒、止血、抗氧化、消除自由基、抑制突变和抗肿瘤等多种生物活性。采用大孔树脂NKA-9从蒲公英中提取绿原酸,绿原酸提取物纯度可达25.3%[24];刘军海等通过对6种树脂进行静态吸附实验,选出NKA-2树脂为吸附分离杜仲叶绿原酸的最佳树脂,产物中绿原酸含量和得率较高[25,26];以聚酰胺为吸附剂,通过聚酰胺柱层析对粗提物进行分离除杂,在优化的工艺条件下,可得到纯度为70%的绿原酸产品[27];山楂叶中含有熊果酸,熊果酸是近年来发现具有强抗癌活性的天然产物,静态吸附结果表明,X-5、NKA和AB-8树脂的吸附率分别为91.32%,72.28%和41.19%;以90%乙醇为洗脱剂,X-5、NKA和AB-8树脂的洗脱率分别为83%,70%,87%[28]。L-脯氨酸是含有亚氨基的中性氨基酸,是构成蛋白质的20种基本氨基酸之一。L-脯氨酸是所有氨基酸中溶解度最大的一种氨基酸,并且是惟一可溶解于乙醇的氨基酸。由于脯氨酸的这一特性,使得纯化精制的难度加大。从发酵液中分离提取脯氨酸的新技术和新工艺对于提高脯氨酸发酵工业的水平和经济效益有十分重要的作用。采用强碱性树脂能够使L-脯氨酸与谷氨酸、蛋氨酸、赖氨酸等杂酸基本分离[29];采用X-5大孔吸附树脂精制甘草酸具有吸附性能好、吸附效率高、再生简单、解吸条件温和、产品纯度高、使用周期长、节省费用等优点,采用X-5大孔吸附树脂精制甘草酸具有广阔的工业前景,产品纯度可达95.2%[30]。
吸附树脂法处理含酸废水是一种较为有效的处理方法,树脂具有物理空隙大、交换速度快、交换容量大、再生率高、耐渗透压、耐冲击变形、耐有机污染性能好、物理强度高等优势。吸附法提取有机、无机酸,具有节约能源、流程简单、除杂效果好、分离效率高、操作费用低、过程无新的污染产生的优点,但缺点是吸附剂寿命低,对于混合酸分离选择性差。
1.2.2 溶液分离方法
目前,国内外针对溶液的分离主要的几种方法见表1-2。
表1-2 有机物分离方法的比较

①沉淀法:该过程是分离极性物质最常用的方法。其原理是在溶液中加入能使极性物质产生沉淀的物质,如金属盐类,然后将沉淀分离,最后还原。通常发酵生产乳酸和柠檬酸中所用的钙盐法,就是沉淀法的一种。该法操作简单,能耗低,但产品收率低,排出固体需处理,并且采用间歇操作,现已逐渐淘汰。
②精馏法:挥发性的有机羧酸,如醋酸,可以从溶液中精馏得到。但是,当醋酸浓度很低时,醋酸和水的相对挥发度接近于1,这时传统的精馏方法就不再是好的选择。目前,对此工业化的处理方法是恒沸精馏和恒沸精馏加溶剂萃取。对于非挥发性有酸溶液,精馏方法则是不可行的。
③膜分离法:这是一种较新的分离方法,它以物质间迁移速度的差别为基础,实现物质间的分离。该方法效率高,无返混,可连续生产,是一种很有前途的方法。目前,在膜的生产和应用中还存在着许多问题,如膜的制备、寿命、浓度极化和膜的污染等问题。
④物理萃取法:物理萃取是不涉及化学反应的物质传递过程,利用溶质在两种不相溶的液相中不同的分配关系将其分离出来。由于极性物质的极性,往往使物理萃取获得的相平衡分配系数D较低。若提高溶剂的极性以增大D值,则溶剂在水中的溶解度增大,会造成较大的溶剂损失,从而使此类方法的应用受到限制。
⑤液体离子交换法:季铵盐常被用于液体阴离子交换物质,作为液膜的载体分子。同离子交换树脂一样,液体离子交换剂在再生过程中会消耗盐或酸。
⑥可逆络合反应分离法:可逆络合反应分离方法是伴随溶质与分离剂之间的化学反应的传质过程。它以其高效性和高选择性而日益受到国内外研究者的关注。利用萃取操作实现此类过程,溶剂的选择、萃取剂的毒性等问题均需认真解决。在许多场合下,利用吸附操作实现此类过程则显得更有优势。固体吸附剂由于不会导致污染而比溶剂萃取法具有潜在的优势[31]。
1.2.2.1 基于可逆络合反应的分离方法
根据“相似相溶”规则,在不形成化合物的条件下,两种物质的分子组成结构愈相似,它们之间的相互溶解度或亲和力就越大,这是选择以物理作用为基础的分离剂的首要原则,然而,这样选择得到的分离剂对于极性溶液的分离常常是不理想的,这是由于溶质和水都是极性物质,若选择极性较大的分离剂,以提高对极性有机物质分离能力,势必同样造成很大的携带水量,这无疑将在工艺过程中带来二次污染或分离剂脱水的负荷。
为了解决极性溶液的分离问题,C.J.King等提出了一种新的分离方法——基于可逆络合反应的分离方法[32]。
以化学反应为基础的分离方法由于其选择性很高而常在分析化学中采用,但工业上以反应为基础的分离方法并不多见,因为具有化学反应的分离过程常消耗大量昂贵的反应剂,反应产物较难回收,而基于可逆络合反应的分离方法则克服了这一缺陷。
基于可逆络合反应的分离工艺过程中,溶液中的待分离溶质与含有特殊官能团的吸附剂相接触,吸附剂与待分离溶质反应形成络合物,使其转移到吸附固相内达到分离的目的。第二步则是进行逆向反应使吸附固相再生以循环使用,而溶质得以回收。十分明显,基于可逆络合反应的分离方法即使在低溶质浓度下也可以提供非常高的分离能力。由于溶质的分离取决于络合反应,络合反应是在特定官能团之间发生的,所以这类方法也具有很高的选择性。
值得提及的是,如何选择基于可逆络合反应的分离方法的分离对象,如何选定分离剂,如何选择溶质回收和分离剂再生方法,是这类分离方法得以实施的关键。
(1)分离对象特性
采用基于可逆络合反应的分离方法,待分离的溶液一般应具有以下特征:
①待分离溶质一般带有Lewis酸或Lewis碱官能团,参与和分离剂的络合反应;
②待分离溶质浓度小于5%(质量分数),此时采用可逆络合反应分离方法具有更大的优势;
③待分离溶质多为亲水物质,在水中有较小的活度系数,一般分离方法难以奏效。
(2)分离剂特性
可逆络合反应分离中使用的分离剂的选择应遵循:
①分离剂应具有相应官能团,与待分离溶质的络合键能应足够大,便于形成络合物,实现相转移;这种络合键能又应相对较低,使络合物容易完成再生时的逆向反应,使分离剂容易再生;
②分离过程应无其他副反应,分离剂应是热稳定的;
③络合反应在其正负反应方向上均应在不同条件下具有足够快的动力学机制,以便使其在实现过程中的设备体积不致过大。
(3)再生方法
可逆络合反应分离过程需根据不同的工艺要求,采用不同的分离剂再生方法。
①如果络合反应平衡常数对温度十分敏感,则可通过温度条件的变化,使溶质从分离剂一相移回到水相中,分离剂得到再生,含溶质的溶液浓缩纯化;
②改变溶液的pH值,加入酸或碱进行分离剂再生,这种方法可以获得浓缩的待分离溶质,但其化学组成可能会出现变化。
(4)可逆络合反应分离过程的特点
对于极性溶液,可逆络合反应分离过程与其他分离过程相比,具有明显的优点:
①高效性。由于分离过程的推动力取决于溶质和分离剂间的化学反应,因此,可逆络合反应分离过程对极性物质的分离效率高,回收率也很高;
②高选择性。分离过程中的化学反应是在分离剂的特殊官能团和被分离溶质的特殊官能团之间发生的,因而选择性很高;
③再生简单,成本低。络合物是可逆化学反应的产物。在一定条件下便可解离,从而得到原来的溶质形态,较容易实现再生。此类操作多数情况可在常温下操作,且可连续作业,便于实现自动化操作和控制,这些对降低操作费用都是有益的。
在溶液的分离方法中,可逆络合吸附法以其选择性好又方便高效成为人们关注的重点。当然,可逆络合吸附操作亦存在着工艺难点,这主要是由于吸附剂种类的限制、固液吸附过程研究工作还欠深入、多组分体系的复杂性和吸附分离操作设备的间断性等因素造成的。这些都有待于进一步研究和开发。
1.2.2.2 吸附分离过程的研究现状
吸附分离作为主要的分离技术之一,有其自己的发展历史。早在两千年以前的古代中国,人们已经学会用木炭吸湿防潮。这说明那时已了解到木炭具有的吸附作用。20世纪50年代以前,吸附剂的种类很少,而且吸附性能差、选择吸附能力低,这些特点决定了它很难适用于大规模的工业化和连续化操作。因此,当时的吸附分离只能在一些辅助设备中以间歇操作进行。化工吸附分离成为大型工业的生产工艺和完整的单元操作过程,是在60年代迅速发展起来的。由于世界能源短缺,急需探索节能的工艺和化工单元操作,同时,对环境污染治理的要求也越来越多,一些新兴的食品和轻工等行业也提出了更高的分离要求,使化工吸附分离这一学科日益得到重视。另一方面,六十年代以来,合成材料有了新的发展,许多性质优良的吸附剂不断出现。在上述两方面的基础上,吸附分离技术得到了突飞猛进的发展,出现了如变压吸附、模拟移动床、色谱分离等一些先进的技术,同时取得了工业装置上的成功。
吸附作为一种单元操作,应该说是比较新的一个过程。以往吸附多用活性炭,包括新发展的碳分子筛,它们虽然具有很大的比表面积,但由于活性炭吸附的机理是多样化的、比较复杂的,往往在使用过程中难以实现很高的选择性。加上如果是固-液接触,与气-液、液-液的不同之处是难以真正实现多级逆流,而往往是一种单级或“错流”操作。高分子合成树脂的出现,为提高这方面的选择性提供了机会。它的特点恰恰在于较为单一的作用机理。如果划分起来,无官能团的大孔树脂主要以范德华作用力为重要机制,而带有官能团的树脂、离子交换树脂,则是通过氢键作用、络合作用(如酸碱反应)和离子交换来实现分离的,具有广泛的应用前景[33]。
(1)固液吸附平衡
吸附平衡一般指在充分吸附接触时间下,吸附质分子和吸附剂表面结构上的原子经能量交换后,吸附质分子到达表面的数量和离开表面返回气(液)相中的分子个数相等所达到的平衡。通过讨论在恒温下的吸附平衡,即等温吸附平衡。在气-固或液-固两相的等温吸附平衡中,当两相在一定的温度下充分接触或充分混合时,吸附质在两相中经过长时间的接触达到的平衡是静态的热力学平衡。在流动体系吸附过程中,两相作相对运动,在一定的接触时间下,吸附质最终在两相内的分配量为一定,最后达到动态平衡。一般动态平衡的吸附量比表态平衡的要低,但与实际操作较接近。
从20世纪起,许多学者从不同的模型和学说出发,推导和修正出各种吸附等温方程。由于吸附机理是极其复杂的,这些吸附理论不能同时适用于各种各样的复杂现象。只有在特定条件下,一种吸附理论才能适用于一定的吸附剂对某几中吸附质的吸附。
一般说来,吸附可以分为:
①物理吸附,即由范德华力引起的分子间的相互作用力;
②化学吸附,被吸附分子与吸附剂表面的原子反应形成与原来分子结构不同的中间络合物,该过程需要一定的活化能。事实上,物理吸附与化学吸附这一传统的分类方法之间并无严格的界限。
固-液吸附与固-气吸附相比,在机理上要复杂得多。除温度和溶质浓度外,吸附剂和溶质不同都会影响等温线的形状,因为液相吸附中,除吸附剂对溶剂和溶质的吸附外,溶质的溶解度和离子化、各种溶质之间的互相的作用以及共吸附现象都在对吸附作用产生不同程度的影响。
Giles等[34,35]研究一系列等温吸附曲线以后,按这些吸附等温线离开原点最近一段曲线的斜率变化,把吸附等温曲线分成四大类。
①S曲线。被吸附分子垂直于吸附剂表面,吸附曲线离开原点后的一段向浓度坐标轴方向凸出。
②L曲线。正规的或Langmuir型吸附等温线。被吸附分子吸附于吸附剂表面或平行状态,或是被吸附离子之间有特别强的相互作用力,而成为垂直的方位。
③H曲线。高亲和力的吸附等温线。该曲线离开原点后向吸附量坐标方向高度凸出,低亲和力的离子为高亲和力的离子所交换。
④C曲线。恒定分配线性曲线。被吸附物质在溶液和吸附剂表面之间有一定的分配率,吸附量的大小与溶液浓度之间成直线关系。
上述的分类方法是按照吸附等温线离开原点后曲线形状的变化、斜率的改变和曲线平坡线段的特点分类的。如果形成单层溶质分子的吸附后,它对溶液中溶质分子的吸附力很弱,则曲线有一段长的平坡地段。如果生成的吸附层溶液中溶质有较强的作用力,则曲线陡升不产生平坡线段。
(2)可逆络合吸附分离的研究
目前就溶液吸附过程的研究而言,关于其吸附平衡的研究报道得较多。对极性溶液而言,分析吸附过程的吸附剂与吸附质间的作用力大体上可分为四种:离子交换、离子对、氢键、范德华力。研究较多的是范德华力和离子交换,而吸附过程中的离子对作用和氢键作用则研究较少。利用这两种作用力来实现不同组分的分离,也较少涉及。
1987年,Y.Kuo、C.L.Munson、M.Frierman等人[36,37]以活性炭和树脂为吸附剂进行了从醋酸-水溶液中吸附分离醋酸的研究,讨论了影响吸附容量的因素、影响选择性的因素、吸附剂解吸等三方面的问题。在大量测量各类吸附剂比表面积的基础上,定性分析了比表面积、碱性官能团、pH对吸附容量和选择性的影响。
1989年,A.A.Garcia等[38]用碱性吸附树脂研究了醋酸稀溶液的吸附,提出了如下假设:①络合分子数比为1∶1;②稀溶液中溶质活度为常数;③所有碱性点具有相等的碱性和可近性;④碱性点数目为常数;⑤活度系数为常数。则可近似用如下所示的理想模型来表达该吸附过程:
B为一个碱性官能团。
1990年,T.M.Grant和C.J.King[39]一起研究了为何含酚物质难于从活性炭上解吸的原因,提出该过程不可逆的原因是因为酚上的氧在活性炭表面发生了化学偶联反应,并与实验结果进行了比较。
1990年,G.F.Payne和Y.Ninomiya[40]分析了基于氢键基础上的选择性吸附,实验选用了聚羧酸脂吸附剂:XAD-7。结果表明,该过程的产生是由于溶液中提供质子的基团和吸附剂中接受质子的羧基之间形成氢键。溶质根据其组成氢键的能力可以被选择性地吸附在中性聚羧酸脂吸附剂上,选择吸附的分离因子依赖于单个溶质的氢键作用力。此外他们应用热力学模型精确地解释了单个溶质的吸附结果,并且根据单个溶质的吸附信息来预测从混合物中吸附某种溶质的选择性,同时肯定了由于氢键作用大小的不同从混合物中分离溶质的可能性。
1991年,N.Maity等[41,42]对溶质和吸附剂之间不同氢键作用的差异进行了研究并测量了吸附亲和力随焓变变化的关系。
1994年,H.Yoshida等人[43]研究了BSA在DEAE-dextran(DEAE为一种弱碱性葡聚糖型离子交换树脂)上的吸附平衡。当pH≥5.05时,它满足Langmuir方程;当pH=4.8时,满足Freundlich方程。实验表明,吸附平衡基本与BSA初始浓度无关,但随着pH值的增大,其饱和吸附量较小。推测当pH大于pH1时,BSA靠静电力吸附;而当pH约等于pH1时,则靠疏水作用或氢键作用。
1995,G.F.Payne和S.Ramakrishman研究了运用萃取和吸附耦合以提高选择性和吸附分离效果的可能性。指出从水中提取非极性物质是依靠离子对形成的静电作用和疏水作用,而从溶剂中把离子对吸附到树脂上是靠极性作用。运用“化学理论”[一般用于当化合物的相互作用力是由极性的“化学”力引起,而不是由能量较低的物理作用力(尤其指范德华力)引起]和线性自由能关系可以较好地反映体系的物理现象。论文证明了在加入非极性的溶剂,如己烷,和低pH值的情况下从水溶液中分离酸性物质的可行性。通过与其他提高吸附选择性的方法比较,设计出具有特殊结构的吸附剂,对于大范围内的低价值的产品的分离是一个经济可行的方案。
吸附过程及吸附平衡的达到与吸附剂化学表面的形状及分布情况是密切相关的。对于带有官能团的树脂,其活性表面的分布就是官能团的分布。选择适当的研究体系,进一步了解吸附剂与吸附质的相互作用,利用新的手段和工具对吸附剂的活性表面进行更深层次的研究,这对于我们研究可逆络合吸附过程有很大的帮助。
(3)液相活度系数的确定
在实际工作中,遇到的待分离混合液往往浓度较高,属非理想溶液。为准确描述溶质在吸附剂上的吸附行为,必须以活度来表示液相溶质的含量,这就涉及到活度系数的计算。
Debye-Huckel在1923年提出了电解质溶液中“离子相互静电作用的模型”,用微观的分析方法成功地阐明了电解质稀溶液的热力学性质与理想溶液发生偏差的原因,建立了活度系数的极限理论。
(1-1)
当离子强度Im<0.005mol/kg,Debye-Huckel极限定律计算电解质的活度系数偏差较小。但当离子强度增大时,理论计算值与实验值要发生较大偏差。近代电解质理论研究者在实验的基础上,对Debye-Huckel公式进行了修正。Bromely的修正式为:
(1-2)
其中Bm与温度有关,a值与电解质的类型有关。
Bromely也提出了多组分电解质溶液的活度系数的修正式为:
(1-3)
式中B为Bromely作用参数,A=0.511。
从1973年以来,Pitzer建立了半经验的统计理论。在Debye-Huckel理论的静电效应势能的基础上,引进了硬心动力效应(离子间的排斥能),这是它的理论基础。他认为离子间的作用能有三种势能:第一种是离子间的长程静电势能;第二种是短程“硬心效应”(hard core effect)的势能(主要是排斥能);还有三个离子间的作用能,这只是在极高浓度时才起作用。Pitzer对高浓度电解质溶液建立了如下活度系数表达式:
Davies建立的计算液相活度系数经验公式,方法如下:
(1-4)
(1-5)
(1-6)
A=1.825×106(εT)-3/2,其中水的介电常数ε=78.30F/m,25℃时,A=0.5115。
该法适用于溶液离子强度I≤0.5mol/L的情况[44,45]。
(4)吸附动力学模型
吸附质由液相主体到与吸附剂上的活性吸附位结合需要经过如下三个步骤:
①吸附质从液相主体通过液膜扩散到达吸附剂粒子外表面;
②吸附质在吸附剂颗粒中的表面扩散和孔隙内扩散,即内扩散;
③吸附质与吸附剂活性吸附位发生结合反应。
如果同时考虑这些步骤对液固传质速率的影响,传质模型将极为复杂,而且由于在大规模的实际分离操作中,所用的吸附剂粒子具有一定的粒径分布,同时活性吸附位在粒子孔内的分布通常也较均匀,这些都导致获得精确模型非常困难,甚至是不可能的。一般情况下,由于各传质步骤的快慢不同,有些步骤传质速率非常快,传质阻力很小,不是主要速率控制步骤,可以不予考虑,而只研究传质阻力比较大的主要速控步骤,以大大简化吸附传质速率模型[46]。
针对不同的吸附体系,常用的简化速率控制模型有如下几种。
①表面吸附反应控制 该模型假定表面吸附反应速率与液膜及内扩散相比很小,则吸附剂粒子内外溶质浓度均一。在实际吸附过程中,表面反应速率与吸附剂内外传质速率相比要快得多,只有在吸附反应速率非常缓慢的情况下,表面吸附反应才有可能成为控制步骤。
②液膜扩散速率控制 该模型假定粒子外表面的液膜传质速率为控制步骤,因此粒子内吸附质浓度均一,这种模型只适用于吸附剂粒径很小或吸附质的内扩散系数极大的情况。
③内扩散速率控制 在大多数实际吸附过程中,表面吸附和液膜传质速率相对较大,因此很少单独考虑表面吸附或液膜传质速率为控制步骤,而认为内扩散为速率控制步骤,有时也同时考虑内扩散和液膜传质或表面吸附。
内扩散控制模型种类很多,但常用的主要有以下几种:
a.固相扩散模型(Solid-Diffusion Model)[47]。假定吸附剂粒子具有均匀的网络结构,而不考虑吸附剂粒子的多孔性质。认为吸附在粒子的外表面发生,在粒子内部吸附质以扩散的形式传递,不区分吸附质是吸附在粒子内表面还是存在于孔内溶液中,仅考虑粒子在表面吸附达到平衡。此模型可用Fick第二定律描述:
(1-7)
式中,De为固相内吸附质有效扩散系数;qi为固相内吸附质的局部浓度;r为粒子半径方向的距离。
b.孔扩散模型(Pore-Diffusion Model)。它是另一种内扩散模型,他认为吸附剂具有多孔结构,它将固相中的溶质分为吸附溶质和孔内溶质,吸附在孔壁面上发生,这是与固相扩散模型不一样的。表达式为:
(1-8)
式中,cs,i为孔内浓度;εi为粒子孔隙率;Dp为孔内扩散系数。另外模型假定在孔内任何时刻和任何位置之间满足吸附平衡关系,即:
(1-9)
式中,f表示吸附等温函数关系。
与固相扩散模型相比,孔扩散模型更切实际地描述了吸附剂的多孔特性,但孔模型的平衡关系式往往是非线性的,且模型形式复杂,使得在预测扩散控制步骤时存在许多不便[48]。由于本研究不需要精确知道吸附体系的动力学吸附行为,只是以此来粗略确定吸附控制步骤,以指导床层吸附行为,所以我们选择简单的固相扩散模型来进行动力学研究。
c.收缩中心模型(Shrinking Core Model)。该模型假定在吸附剂已吸附区和未吸附区之间存在一明显的界面,吸附速率由吸附质通过已吸附壳区的扩散控制。该模型的缺陷是假定吸附质与吸附剂吸附位之间的表面吸附反应为不可逆过程,这个假定在通常条件下与实际不符。如酸在弱碱性树脂上的吸附,由于在吸附过程中在吸附剂孔壁面处存在双电层,双电层上的H+对后续的H+有静电排斥作用,从而使吸附平衡时液相中的H+不能完全扩散到吸附剂上,即 (Q为吸附剂饱和吸附容量),即吸附过程为可逆吸附。收缩中心模型的表达式为:
(1-10)
式中,X为吸附剂的吸附分率;DHA为HA在吸附剂内扩散系数;R为吸附剂半径;[H]为液相H+浓度。
d.改性收缩中心模型(Modified Shrinking Core Model)。该模型保留了传统收缩中心模型简便和准确的特点,弥补了传统模型的缺陷,将可逆吸附引入到模型理论中,获得的模型表达式为[49]:
(1-11)
式中,Xe为平衡时吸附剂吸附容量。改性收缩中心模型可用来准确描述吸附剂在吸附质内的动力学吸附行为。
e.反应速率方程(Reaction Rate Equation)。现有的反应速率模型较多,常用的主要有一级反应速率模型,二级反应速率模型[50,51]。
一级反应速率模型,又称Lagergren方程,其表达式:
(1-12)
二级反应速率方程表达式:
(1-13)